Polyplast
Fabrication de Pièces en Polyuréthane
NOTRE EXPERTISE
L’optimisation de l’efficacité dans les secteurs minier, forestier et manufacturier.
Nos solutions robustes permettent de limiter les arrêts imprévus pour optimiser votre production et garantir un retour sur investissement !
Nous contribuons à prolonger la durée de vie des composants et des équipements, réduisant ainsi la surconsommation. Nous nous engageons à trouver des solutions innovantes pour permettre l’atteinte de vos objectifs.
Notre mission
Offrir des solutions innovantes et robustes en favorisant l’efficacité. Notre priorité est de maintenir des normes élevées de fiabilité et de confidentialité tout en réduisant la surconsommation.
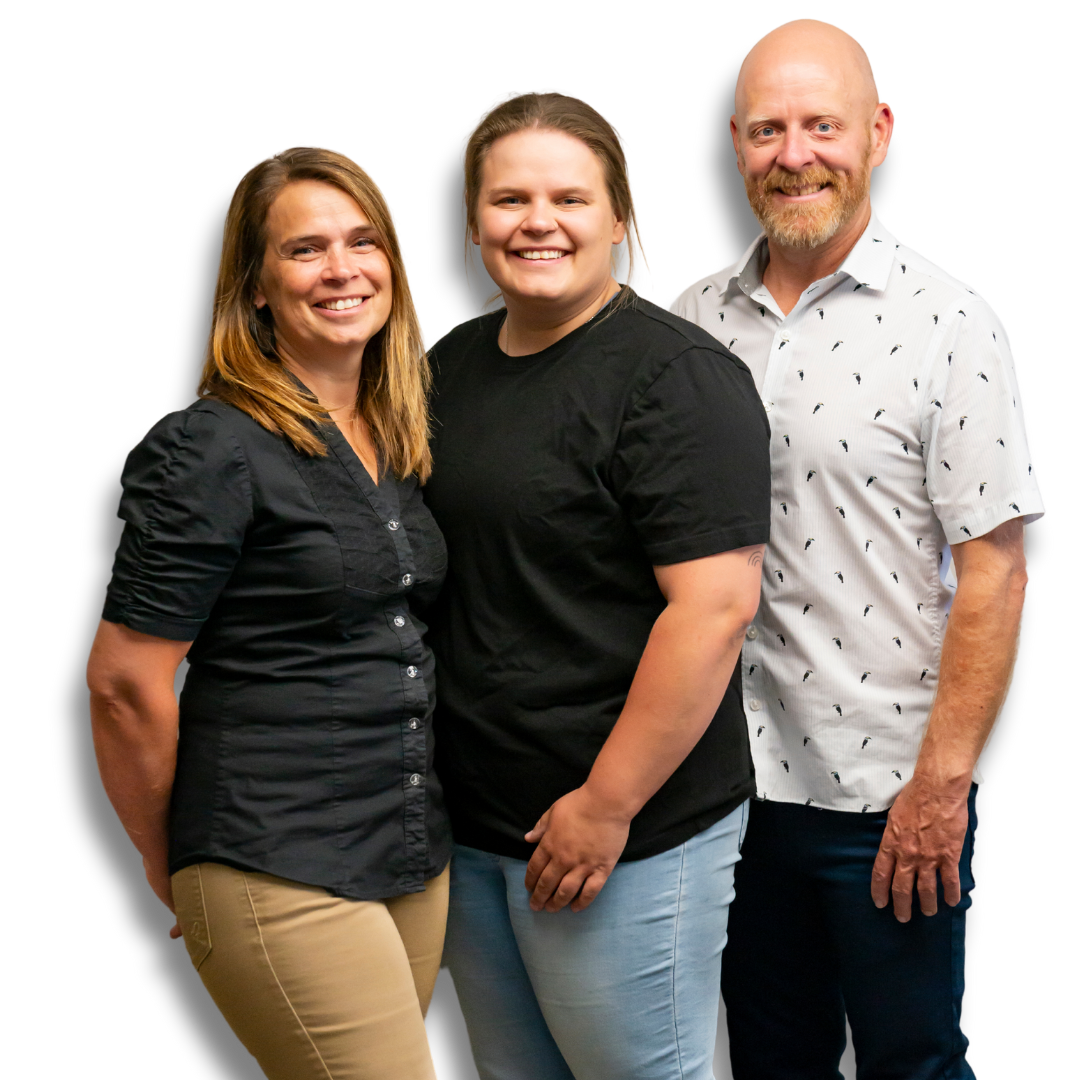
LES PRODUITS POLYPLAST, C’EST…
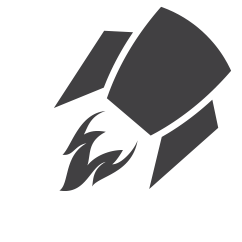
Vitesse
L’utilisation du Polyplast à des endroits stratégiques permet d’accroître votre productivité.
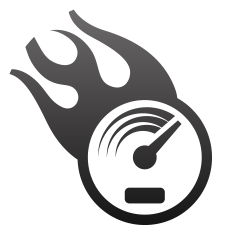
Longévité
L’utilisation de matériaux résistants permet de garantir ainsi une performance optimale et une meilleure rentabilité.
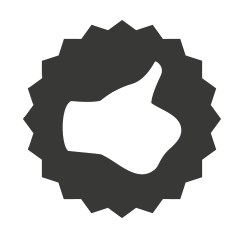
Qualité
Notre solution améliore la qualité des produits manufacturés en réduisant les vibrations, contrer l’abrasion et les impacts nuisibles à vos activités.
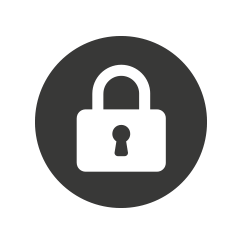
Sécurité
Notre méthode de conception constante et fiable nous permet de répondre à divers besoins en matière de sécurité.
Notre solution Polyplast est conçue pour prolonger la durée de vie de vos équipements, optimiser votre production et garantir un important retour sur investissement.
MICHAËL LAVOIE, CO-PROPRIÉTAIRE
Témoignages
Polyplast a su nous écouter et nous conseiller dans le développement d’un nouveau produit pour une nouvelle application. Ils nous ont aidés dans le prototypage et ont réagi rapidement lors de l’élaboration de solutions quand nous avons rencontré des problèmes. Grâce à Polyplast, nous avons trouvé des solutions durables et avons rapidement satisfait nos clients ! Ils partagent nos valeurs d’agilité et d’engagement envers les clients, ce qui, comme nous, les démarque de leurs compétiteurs! Merci!
- Matthew Mercier
Directeur ingénierie, Rotobec
Depuis plus de 20 ans, CMAC-Thyssen et Polyplast entretiennent une relation de partenariat solide et durable, marquée par une fiabilité exceptionnelle et un soutien constant.
Polyplast a continuellement démontré son engagement envers la qualité et son adaptabilité aux besoins évolutifs de notre entreprise, ce qui en fait un partenaire essentiel à notre succès.
- Guillaume Julien
CMAC-THYSSEN
Nous aimons faire affaire avec Polyplast car nous avons un service professionnel et des réponses rapides aux courriels !
Il est important pour nous de travailler avec des fournisseurs locaux.
- Patrick Desputeau
Planificateur, Agnico Eagle
Nous avons développé plusieurs produits ensemble. Ils sont toujours disponibles pour trouver des solutions et ce depuis 25 ans.
- PLC INC
AU-DELÀ DU POLYURÉTHANE
Une innovation qui décuple la précision et la performance
Nous le savons tous, les percées scientifiques se font presque toujours dans l’ombre. Pensons à ces chercheurs qui s’affairent à réaliser des projets, à l’abri des regards, dans des instituts de recherche ou des laboratoires. Nous avons décidé de mettre en lumière nos...
Le polyuréthane, une ressource des plus étonnantes
L’utilisation du polyuréthane s’étend à de plus en plus de domaines, et les applications ne cessent d’évoluer grâce aux progrès dans sa composition. Ce matériau contribue à améliorer une panoplie de produits d’usage autant domestique qu’industriel. Selon des...
Le polyuréthane, le superhéros des matériaux et le champion des solutions
Le polyuréthane ne cesse de nous épater, tant par ses usages que par ses propriétés. Le polyuréthane est partout; il fait partie intégrante de notre quotidien sans que nous le sachions. Que ce soit comme scellant ou comme isolant thermique, pour ses propriétés...
Le polyuréthane – une solution pour le colmatage et l’abrasion
Le polyuréthane est un matériau polyvalent et d’une grande malléabilité qui offre une foule de possibilités. Il est également très résistant et permet de trouver des solutions à la fois originales et efficaces qui éviteront des interruptions de production fort...
Les solutions en polyuréthane – d’intéressantes pistes d’avenir
Dans notre dernier article de blogue, nous vous présentions comment le polyuréthane se taille une place comme solution pour le colmatage des tuyaux. Nous avons aussi découvert que ce matériau des plus polyvalents constitue une solution de choix pour ce qui est de la...
Le Polytapis, une autre innovation signée Polyplast
Le polyuréthane est un matériau qui peut être approprié et très performant dans une foule d’applications, car il offre résistance et durabilité pour contrer l’usure, l’abrasion, les chocs et la rouille. Au cours des années, nous avons créé des pièces de polyuréthane...
Polyplast : les affaires vont bien!
En activité depuis plus de vingt ans, Polyplast continue de prendre de l’expansion. En fait, chez Polyplast, ça ne cesse de bien aller! Servant déjà des clients fidèles des domaines minier, forestier, manufacturier et agricole, nous en accueillons toujours de...
POLYPLAST CRÉE UNE SOLUTION QUI PROTÈGE, MÊME SOUS TERRE
Chez Polyplast, inventer et créer des solutions inédites en polyuréthane, c’est notre raison d’être et notre passion. Il n’y a rien de mieux que de voir un client repartir de chez nous avec la solution qui comble ses attentes! Pour ce faire, nous demeurons toujours à...
Polyplast repousse les limites dans le secteur minier
De par son positionnement en tant que figure de proue en matière de fabrication de pièces en polyuréthane au Québec, Polyplast se donne comme mission de constamment innover et d’offrir toujours plus de solutions inédites à sa clientèle. Encore une fois, nous...